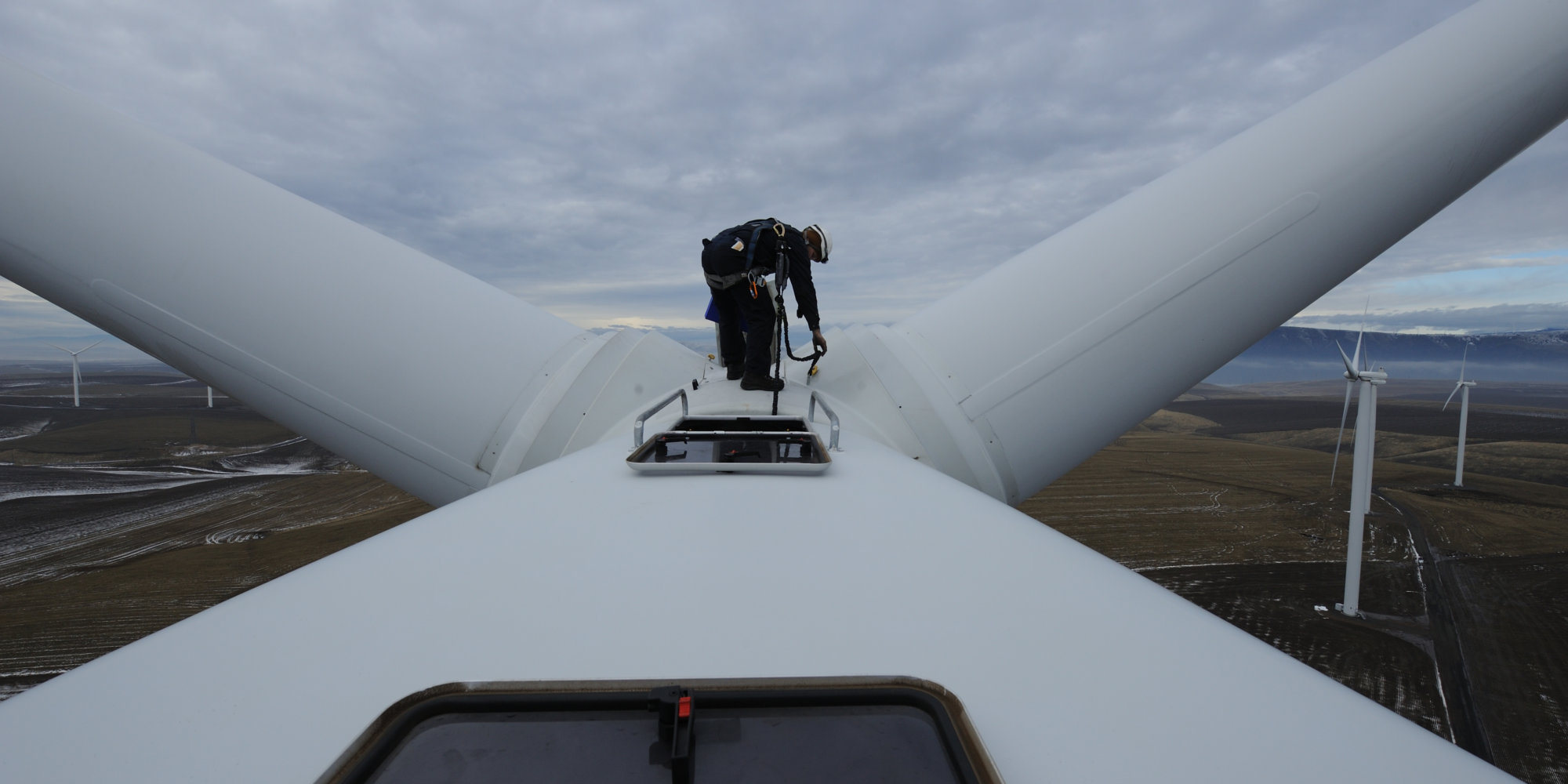
Hello, my name is Russell Carr and as I mentioned in the previous video, throughout my career as a small business owner and entrepreneur I’ve lived through many of the same environmental, health and safety compliance challenges that you’re probably facing today.
We created this video to tell the story of how I really struggled with implementing and managing a workplace safety program with one of my past companies, and how those experiences inspired me to start a new company called Berg Compliance Solutions which is dedicated to helping other small business owners and small companies achieve and manage OSHA AND environmental regulatory compliance.
So here’s what’s really important to understand and why you should continue watching this video if your end goal is to achieve compliance for your company.
My struggles included making a lot of compliance related mistakes that ended up preventing my company from ever achieving true OSHA compliance and implementing a sustainable workplace safety program for the company. These mistakes also ended up leading to my company getting inspected and fined by OSHA in 2010 for not having a confined space program. And I hate to admit it now, but at the time, I didn’t even know that we needed one, but I’ll talk more about that later.
But what’s also really important to understand is that I later found out that a vast majority of other small businesses end up making many of the exact same mistakes that I made, which of course prevents them from achieving compliance too. I saw this play out first hand over and over again with competitors of my energy services companies as well as clients of my hazardous waste management business.
You see, there’s a very defined and proven process that a company must follow in order achieve compliance, and if they follow that process, they’ll almost always succeed. But the problem is that these common mistakes that I’m about to talk about almost always end up popping up with small companies, and end up derailing and undermining that process so badly that the company never ends up achieving their compliance goals. And to make matters worse, the company almost never realizes this until it’s too late, and by too late, I mean until after they’ve been inspected and fined by a regulatory agency like happened to me, or after an employee gets seriously injured or some other costly disaster happens.
So again, seeing how this whole process can play out, and end up causing major damage to small companies, was one of my main inspirations for starting this company: to help other small businesses avoid these common mistakes and achieve environmental, health and safety compliance.
So stick around for a few minutes to check it out. I’ll be you can relate to a lot of the things I’m about to talk about, hopefully, learn from my experiences and mistakes, but most importantly benefit by getting a better understanding of what needs to be done to finally tackle all of your compliance challenges.
Before I go any further, It doesn’t matter if you’re in manufacturing, construction, industrial services, energy, distribution, healthcare or even retail, this story still applies to you. Believe me when I tell you.
Which finally brings me back to the photo of the guy on top the wind turbine from the first video.
The technician was an employee of a wind energy services company that I used to own and operate, and although you can’t see me, I was the guy who took this photo while we were working on a wind farm on the Columbia River Gorge in western Oregon in 2011.
The main point of this photo is to set the stage for the story by illustrating the extreme dangers of the work that we did.
To give you a better idea of the extreme fall danger, here’s another photo that I took that day of other nearby turbines on the wind farm. If you’ve never been up close to a utility scale wind turbine, they’re incredibly massive and complicated machines.
So now that you have a better idea of what I was dealing with and all of these safety challenges and risk, let’s rewind around 4 years prior to the day I took this photo, to 2007 when I originally decided to start the company.
At that time the wind business was booming, and there was sort of a gold rush mentality. I did a lot of research before starting the company and learned that there were many other small service companies like mine popping up all over the place trying to take advantage of the opportunity. What I also learned was that many, if not all of them, paid little if any attention to safety. They typically just bought their technicians some fall protection equipment, hard hats and safety glasses and shipped them off to wind farms without any formal safety training or knowledge.
I was well aware of this problem and determined not to make the same mistake, but at the same time didn’t really know what to do. To put it another way, at that point in time I didn’t understand OSHA regulations, let alone how to implement and manage them.
Despite my ignorance regarding workplace safety, I knew that something needed to happen before we started wok, so I ended up organizing a sort of “safety orientation course” with the help of a community college in northern Iowa who specialized in training wind turbine technicians. The idea was that all of my future employees would need to attend this training prior to starting work. The training was a 2 day course that combined class room time at the school as well as practical time in a wind turbine near the campus that the school operated. Here are a few pictures from that initial training course.
- Here’s a picture of the guys who attended that first training session, and ended up becoming some of my first employees.
- Here’s another picture of me on top the wind turbine that we trained on. This was the first time I’d ever climbed a wind turbine so I spent a long time up there really trying to soak it all in.
- Here are a couple of more photos I took that day of the ground far below to give you a better idea of the extreme height and what I experienced that day. I’m not going to lie to you, it was really terrifying stuff especially for someone like me who’s afraid of heights.
- And here’s another one from the inside of what’s called the nacelle, which is the top piece of the turbine. As you can see it’s a small, cramped area and is considered to be a confined space by OSHA, but I didn’t know that at the time.
And here’s another look at the picture of me sitting on top the turbine. Notice that I’m sitting, and not standing and there’s a reason for that, I was really scared!
The whole experience was a real eye opener and not only made me realize how incredibly dangerous our work was going to be, but also the huge responsibility that I now had to help ensure that our employees were safe and would never be injured or god forbid, killed while working for the company. It was a very sobering experience and for a minute actually made me stop and wonder what I was getting myself into.
4 years later I founded another energy service company in the oil and gas industry, and had a very similar experience while watching a team of our employees connecting a set of tanks on a drilling pad in preparation for a frack in south Texas. I’ll never forget watching them swinging sledgehammers while standing right next to each other, while huge trucks moved backwards and forwards across the tiny pad. It was an incredibly crowded and dangerous work environment, which gave me that same sense of dread, concern and responsibility that I felt that day on top of the wind turbine.
In each of those moments I made myself the same commitment, which was literally that “none of my employees were going to get hurt or killed on my watch.” In other words, I committed myself to spending whatever time, money and resources that were necessary to achieve this goal. I’ll give myself credit for putting my money where my mouth was by spending literally tens of thousands of dollars on safety equipment, training, and resources during the years I owned the company, but also made a lot of mistakes along the way while trying to figure out how to manage safety at the company.
And believe it or not, I had already made my very first safety program mistake during that 2 day training session that I just talked about, and it was a major one. Maybe some of you already know what that mistake was, but either way I’ll talk much more about it in the next video, and it was only the first of a long list of health and safety related mistakes that I ended up making while owning the company.
Thinking back, it’s incredibly humbling and embarrassing to admit these mistakes, especially knowing what I do now about workplace safety, but it happened and as I’ve found out since then, and mentioned earlier, these kinds of mistakes are all too common with small companies, regardless of the industry..
And again, important thing to understand is that these mistakes were what prevented my company from achieving OSHA compliance and establishing a solid workplace safety program. And I’ll bet that your company is making some if not all of the same mistakes, and until you recognize and over come them, you’re company will remain non-compliant and therefore at risk for not only serious employee injuries or worse, but also major regulatory fines and penalties as well as potential civil and even criminal liabilities if something goes wrong.
And as I mentioned earlier, that’s exactly what ended happening to me, when my company got inspected and fined by OSHA for not having a confined space program. And again, I didn’t even know what that was, let alone that we needed one.
And then around the same time I saw one of my direct competitors also get inspected by OSHA and ended up with a $378,000 fine after one of their employees nearly got killed while working on an electrical transformer. This ended up literally being the 10th largest fine that OSHA issued that year in the entire country. And not only did they get fined, but also got added to something called the Severe Violator Enforcement program, which is a nasty long term enhanced enforcement program that OSHA puts many small businesses into.
I knew all to well that if it happened to them, it could just as easily happen to me.
And when it happened, word spread quickly and within a few days the entire industry knew about it which turned into a major PR disaster for the company. They were a much larger company and somehow managed to survive the ordeal, but if it had happened to me, it would have literally destroyed my company and everything that I’d worked so hard for.
So this is what’s at stake and what these common mistakes can lead to, so take a few minutes to watch these videos, I’ll bet you’ll learn a lot from my mistakes and may even end up saving your company from one of these disasters.
I’ve broken my story up into several short videos. Each one talks about a specific mistake that I made while trying to manage safety at the company, and then I’ll relate it to similar mistakes that we’ve seen other small companies make. Keep in mind that we see these same mistakes over and over again with other small businesses, so there’s a good chance that your company has made them too or will in the future.
And in the final video, I’ll summarize all of these mistakes and then talk about how we’ve helped many of our clients overcome and solve them, as well as other safety challenges and ultimately become compliant with all of the environmental, health and safety regulations that impact their businesses and how we do this in the most cost effective and least disruptive way for our clients.
But if you already know that you need help and want to reach out for a free consultation, or just to ask some questions about your company’s safety program, feel free to give us a call at 512-457-0374 or send me an email. We’ll get right back in contact to answer your questions and get you some help.